Plastic Recycling To Rebuild To PET PP HIPS Sheet Or Roll
August 1, 2024
News
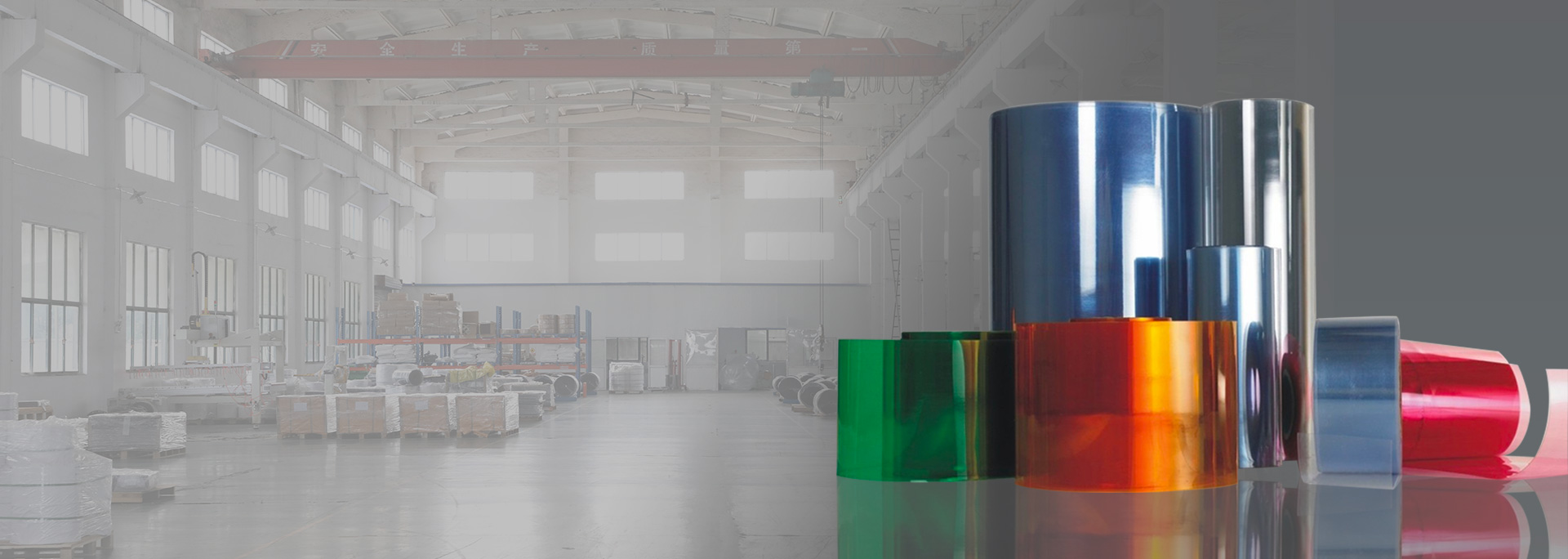
The recycling process to rebuild PET (Polyethylene Terephthalate), PP (Polypropylene), and HIPS (High Impact Polystyrene) into sheets or rolls involves several key steps. Each plastic type has its unique characteristics, and recycling methods need to be tailored accordingly. Here’s a general overview of the recycling process for these plastics:
1. Collection and Sorting:
- Collection: Used plastic items, such as bottles, packaging materials, or other products made from PET, PP, or HIPS, are collected from various sources, including recycling bins and collection centers.
- Sorting: The collected plastics are sorted based on their resin types. Advanced sorting technologies, including automated systems and manual sorting, help separate PET, PP, and HIPS from each other and from other plastics.
2. Cleaning and Shredding:
- Cleaning: The sorted plastics undergo cleaning processes to remove contaminants, such as labels, adhesives, and any residual contents. This step is crucial to ensure the quality of the recycled material.
- Shredding: Cleaned plastics are then mechanically shredded into smaller pieces or flakes. This increases the surface area and facilitates the subsequent melting and extrusion processes.
3. Melting and Pelletization:
- Melting: The shredded plastic flakes are melted at high temperatures. Each type of plastic (PET, PP, HIPS) requires specific temperature ranges for melting.
- Pelletization: The melted plastic is then extruded through a die to form small pellets. These pellets serve as the raw material for manufacturing sheets or rolls.
4. Sheet or Roll Production:
- Blending (Optional): Depending on the desired properties of the final product, recycled PET, PP, and HIPS pellets may be blended in specific ratios or used separately.
- Extrusion: The recycled plastic pellets are fed into an extruder, where they are melted and formed into a continuous sheet or roll. The extrusion process involves shaping the material using a die.
- Cooling and Sizing: The extruded sheet or roll is then cooled to solidify the plastic. After cooling, it may go through sizing processes to achieve the desired thickness and dimensions.
5. Quality Control:
- Testing: The recycled sheets or rolls undergo quality control tests to ensure that they meet the required specifications, including thickness, strength, and other relevant properties.
6. Application-Specific Processing (Optional):
- Additional Processing: Depending on the intended application, the recycled plastic sheets or rolls may undergo additional processing steps, such as printing, embossing, or lamination.
7. Distribution and Use:
- Market Distribution: The final recycled PET, PP, or HIPS sheets or rolls are ready for distribution to manufacturers or businesses that use them for various applications, such as packaging, construction, or other industries.
8. End-of-Life Considerations:
- Recyclability: When the recycled sheets or rolls reach the end of their life cycle, they can be collected and recycled again, contributing to a more sustainable and circular approach to plastic use.
CONTACT PET-SHEET.COM
Our professional sales staff and technicians will determine the final characteristics of the product and material solution for the customer specific application and will provide the customer with a quote and a detailed time schedule, Please fill the form to contact our professional sales team.- Main Category
- APET Sheet Roll
- ESD Antistatic PET Sheet Roll
- GAG Sheet Roll
- PETG Sheet Roll
- RPET Sheet Roll
- Thermoforming PET Sheet Roll
- Latest Products