Why should the surface of PET plastic sheet roll be coated with silicone oil?
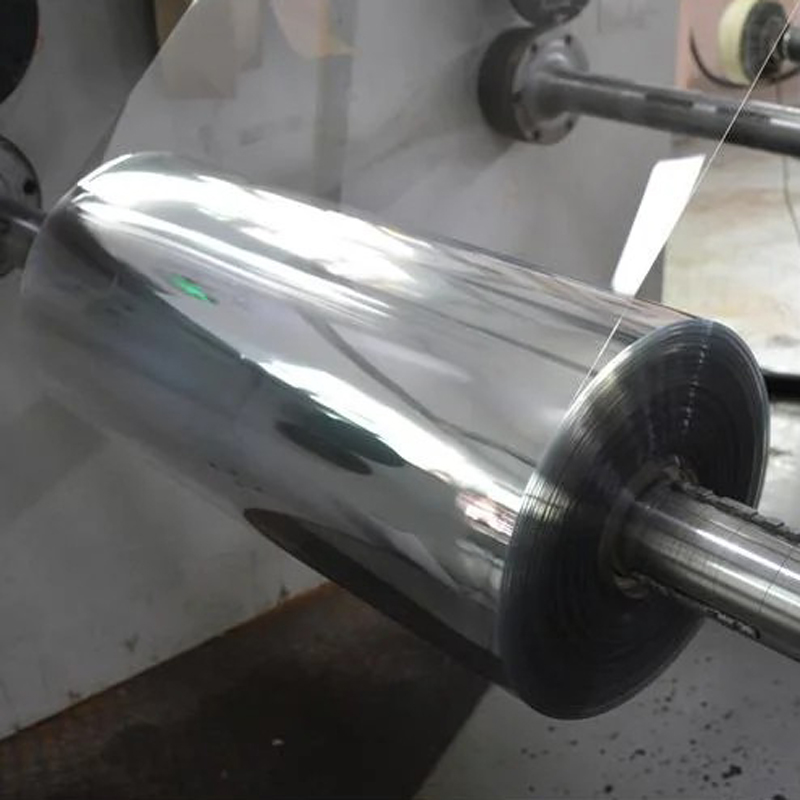
Function of applying silicone oil on the surface of PET plastic sheet roll
Coating the surface of PET (Polyethylene Terephthalate) plastic sheet rolls with silicone oil serves several important functions:
1. Anti-blocking: Silicone oil creates a thin, slippery layer on the surface of the plastic sheet rolls, which prevents the sheets from sticking together when rolled or stacked. This is particularly useful during manufacturing, handling, and storage.
2. Improved Slippage: The silicone coating reduces the coefficient of friction on the plastic sheet roll’s surface, making it easier to handle, unwind, or process the sheets in high-speed operations, such as printing or laminating.
3. Anti-scratch: Silicone oil can provide a protective layer that minimizes the risk of scratches during handling and processing. This is important for maintaining the visual and structural integrity of the plastic sheet rolls.
4. Heat Resistance: Silicone oil has good thermal stability, so it can help the PET sheet withstand higher temperatures without sticking or deforming, especially during processes like thermoforming.
5. Release Properties: In some applications, such as in the production of labels or adhesive-backed products, the silicone coating acts as a release agent, allowing the plastic sheet rolls to separate easily from other materials.
6. Enhanced Optical Properties: Silicone oil can sometimes improve the clarity or gloss of plastic sheet rolls, which is desirable in applications where visual appearance is important, such as in packaging or display materials.
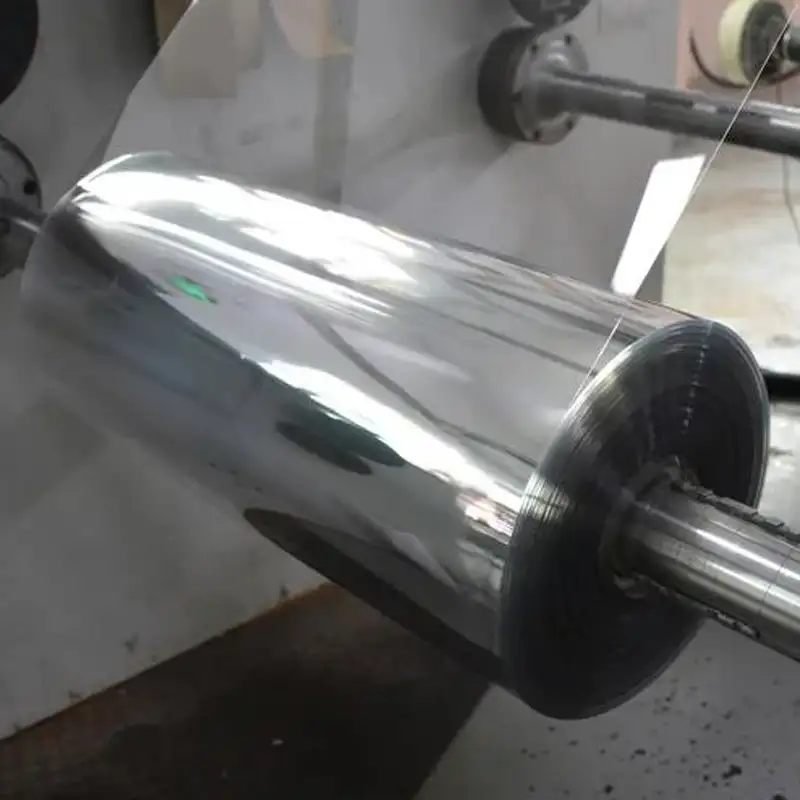
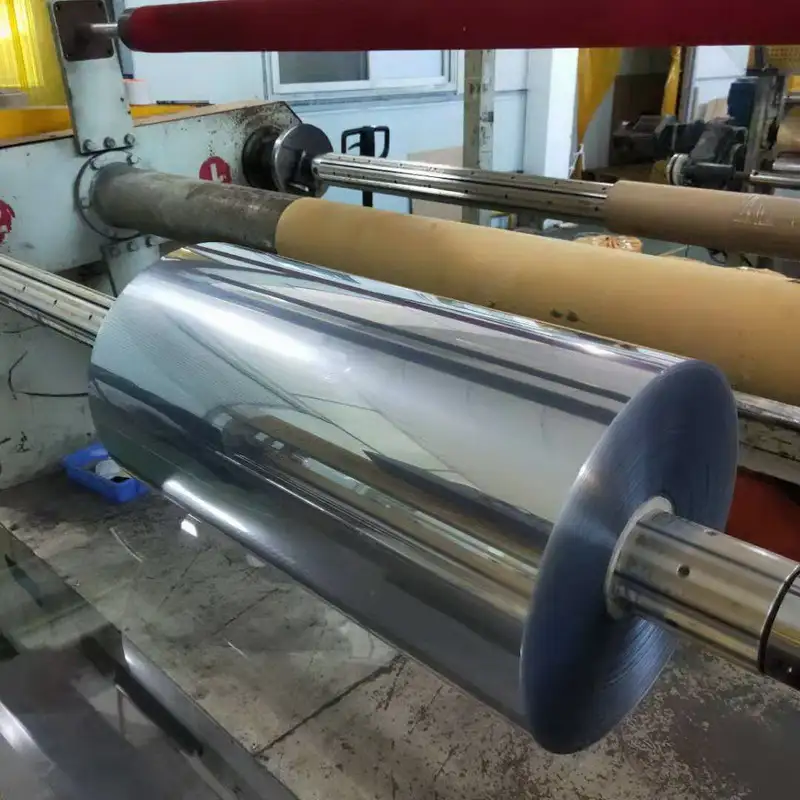
These benefits make silicone oil a valuable coating material for plastic sheet rolls in various industrial applications.
There are mainly the following processes for coating the surface of PET plastic sheets with silicone oil
Silicone oil is usually applied to the surface of PET plastic sheet rolls in the following ways:
1. Roller coating: The silicone oil is applied to the roller, and the PET plastic sheet roll is then pressed over the roller so that the silicone oil is evenly coated on the surface of the sheet.
2. Dry coating: The silicone oil is showered on the surface of the PET plastic sheet rolls, and then the silicone oil is evenly distributed by a scraper or other means.
3. Spraying: Use a spray gun to spray silicone oil on the surface of PET plastic sheet rolls.
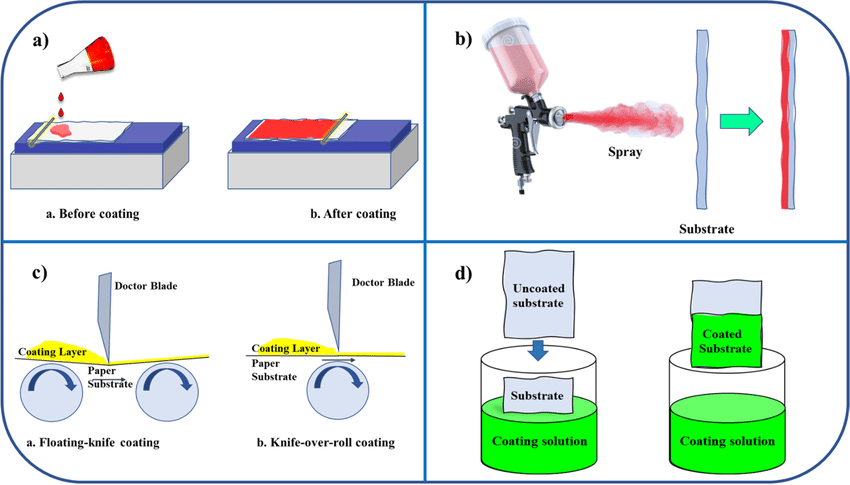
Advantages of using silicone oil in PET plastic sheet rolls
1. Silicone oil has good heat resistance and chemical stability, and can be used in high temperature and harsh chemical environments.
2. Silicone oil is non-toxic, odorless, non-irritating, and safe for human body and environment.
3. Silicone oil has good lubricity and demoulding properties, which can improve the production efficiency of PET plastic sheet rolls.
4. Silicone oil can improve the surface gloss, wear resistance and scratch resistance of PET plastic sheet rolls.
Disadvantages of using silicone oil in PET plastic sheet rolls
1. Silicone oil will reduce the adhesion of PET plastic sheet rolls, so it should be used with caution in applications that require adhesion.
2. Silicone oil will affect the printing performance of PET plastic sheet rolls, so special inks should be used in printing applications.
PET plastic sheet roll surface coating silicone oil process
The process of applying silicone oil as a surface coating on PET (polyethylene terephthalate) plastic sheet rolls is often done to enhance the material’s properties, such as reducing friction, improving release characteristics, or providing a protective layer. Here’s an overview of the process:
1. Preparation of PET plastic Sheet roll
Cleaning: The PET plastic sheet roll surface should be free from dust, oils, or other contaminants to ensure proper adhesion of the silicone coating.
Drying: The sheet may be dried to remove any moisture that could interfere with the coating process.
2. Silicone Oil Selection
Type of Silicone Oil: The choice of silicone oil depends on the desired properties. Commonly used silicone oils include polydimethylsiloxane (PDMS) or modified silicones for specific functionalities (e.g., improved slip, enhanced durability).
Viscosity: The viscosity of the silicone oil is adjusted according to the application method and desired coating thickness.
3. Application Process
Coating Method: Various techniques can be used to apply silicone oil to the PET plastic sheet roll:
Roll Coating: Silicone oil is applied through a roll coater, where the PET plastic sheet roll passes between rollers that evenly distribute the oil on its surface.
Spray Coating: Silicone oil is sprayed onto the PET plastic sheet roll using a fine mist, ensuring uniform coverage.
Dip Coating: The PET plastic sheet roll is dipped into a silicone oil bath and then passed through rollers to remove excess coating.
Control of Coating Thickness: The thickness of the silicone oil layer is controlled by the speed of the roll, the viscosity of the silicone oil, and the gap between the rollers.
4. Curing
Thermal Curing: After the application of silicone oil, the PET plastic sheet roll may be passed through an oven or heated rollers to cure the silicone coating. The curing temperature and time depend on the type of silicone used.
UV Curing: Some silicone coatings are UV-curable, requiring exposure to UV light to initiate the cross-linking process.
5. Post-Coating Treatment
Inspection: The coated PET plastic sheet roll is inspected for uniformity, thickness, and defects.
Slitting and Rewinding: The coated PET plastic sheet roll is slit to the desired width and rewound into rolls for further processing or shipping.
6. Quality Control
Testing: Tests may be conducted to ensure that the silicone coating meets specifications, including adhesion tests, friction tests, and durability assessments.
7. Packaging
Protective Packaging: The coated PET plastic sheet rolls are packaged to prevent damage to the silicone surface during handling and transportation.
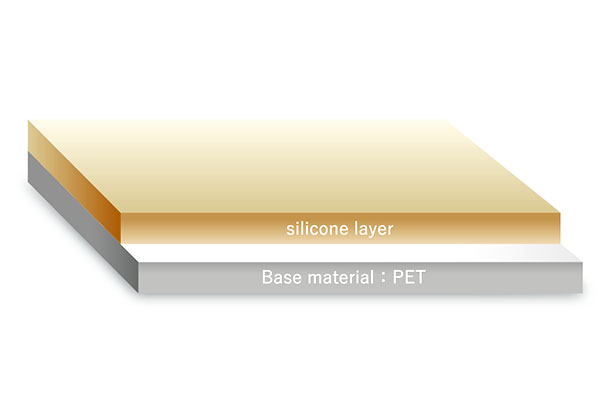
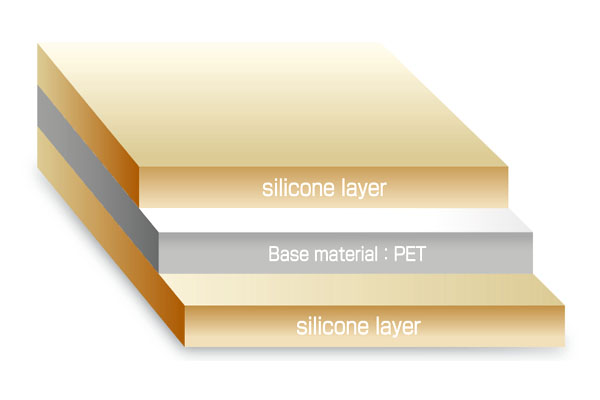
This process provides PET plastic sheet rolls with enhanced performance characteristics suitable for various applications, such as release liners, protective films, or packaging materials.
CONTACT PET-SHEET.COM
Our professional sales staff and technicians will determine the final characteristics of the product and material solution for the customer specific application and will provide the customer with a quote and a detailed time schedule, Please fill the form to contact our professional sales team.- Main Category
- APET Sheet Roll
- ESD Antistatic PET Sheet Roll
- GAG Sheet Roll
- PETG Sheet Roll
- RPET Sheet Roll
- Thermoforming PET Sheet Roll
- Latest Products